Custom metal fabrication begins with a deep understanding of the customer’s unique requirements to develop an approach that delivers the most accurate results of the highest quality.
That’s why Arrow Engineered Products uses specialized fabrication processes to overcome design challenges and meet project specifications. This blog highlights two techniques that help us meet or exceed customer expectations regarding product design requirements and performance: heat transfer in jacketed vessels and autoclave and mixing technology.
Bring On The Heat – Techniques For Maximizing Heat Transfer In Jacketed Vessels
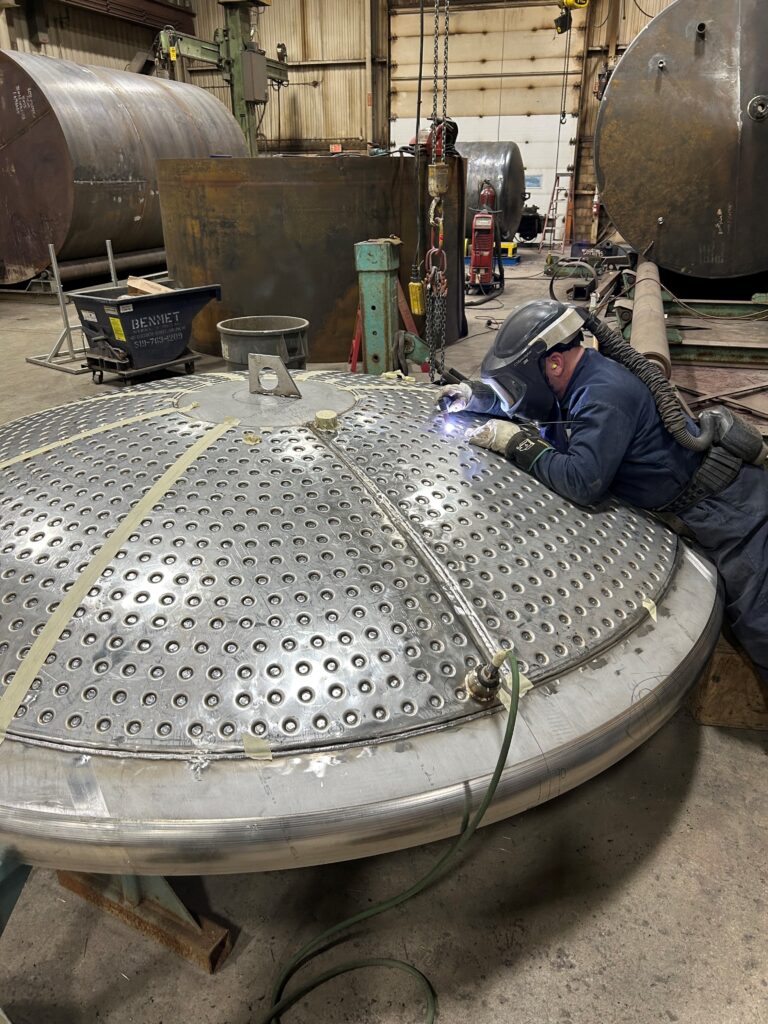
In metal fabrication, jacketed vessels are commonly used to heat or cool the contents inside the vessel. When heating the contents to fabricate a part or component is required, thermal energy is transferred from the external jacket surrounding the unit to the material inside. Advanced temperature control systems and feedback mechanisms allow operators to precisely control the jacketing medium’s temperature.
There are three main methods of heat transfer involved when using jacketed vessels:
Conduction
This method involves transferring heat through physical contact between the vessel wall, which is typically made of metal, and the material inside, providing direct heat application.
Convection
A heat transfer fluid, such as steam, hot water, or other liquids with high thermal conductivity and low viscosity, flows through the jacket. The fluid releases heat from the vessel as it circulates, affecting the temperature of the material inside and providing uniform heat distribution. Many jackets are equipped with baffles or helical coils to promote turbulent flow, prevent laminar flow zones, and ensure consistent fluid circulation.
Radiation
Radiant heat is transferred through electromagnetic waves from the hot surface of the vessel wall to the material inside. This approach is commonly used for high-temperature applications.
Optimizing heat transfer efficiency largely depends on several factors, including the design, thickness, geometry, and conductivity of the jacketed vessel and the flow rate and temperature of the heat transfer fluid. Using materials with high thermal conductivity, such as stainless steel, copper, and aluminum, can also influence the result of the finished product. High-grade insulation may help retain the vessel’s thermal energy, reducing the amount of heat escaping to the surrounding environment.
Many metal fabrication shops use agitators or mixing devices inside the vessel to prevent the formation of stagnant fluid layers, enhancing heat transfer. Specialized heat exchangers within the jacketed vessel can promote more efficient heat exchange.
At Arrow Engineered Products, we tailor our heat transfer techniques to your application’s specific requirements and constraints, taking into account factors such as the type of fluid, operating temperatures, and the overall process requirements. Our design engineers are always happy to give our best recommendations on which heat transfer method would be best for your specific application.
Read More: Our Capabilities
Enhanced Operator Flexibility With Autoclave And Mixing Technology For Metal Fabrication
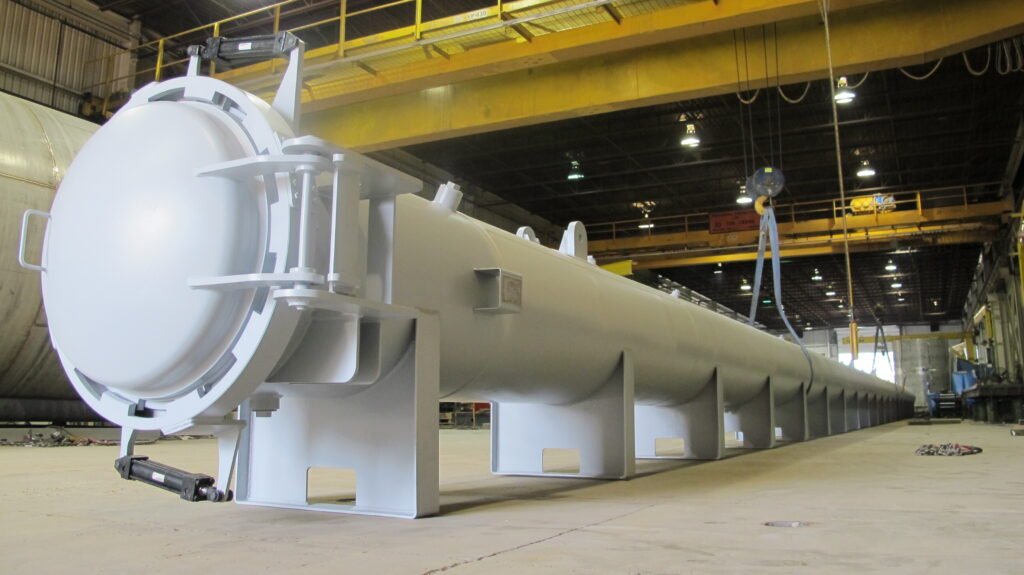
Advancements in autoclave and mixing technology play a crucial role in custom design flexibility, enabling fabricators to bring customers’ design dreams to life.
The autoclave process involves subjecting composite materials to elevated temperatures and high-pressure conditions to achieve curing or bonding, primarily when a combination of metal and composite materials is utilized. Customizable control systems allow operators to adapt the control parameters, such as temperature, pressure, and mixing speed to suit different processes, ensuring optimal performance for various applications.
The design often involves selecting or creating alloys with specific mechanical, thermal, or corrosion-resistant properties. Sophisticated mixing technology allows operators to set precise ratios to achieve the desired material characteristics, ensuring homogeneity in the alloy composition.
Metal design and fabrication shops such as Arrow Engineered Products use these technologies to provide to-spec products for even the most complex design requirements. Modern autoclave systems are designed for simple use through their graphical interface, intuitive controls, and scalability, allowing for changes in production volume or equipment size without requiring significant modifications. The result is higher-performance parts and components and easier installation by the manufacturer.
Collaborate With The Design Team At Arrow Engineered Products
Our team of designers, engineers, and fabricators is committed to recommending cost-effective processes that leverage advanced technology to help our customers meet their manufacturing goals with enhanced efficiency and reliability.
Our ability to connect you with virtually any metal design and fabrication solution makes us the only quality parts and components partner you’ll ever need.
Contact Arrow Engineered Products for high-value design, engineering, and fabrication solutions to suit almost any application. Experience the Arrow difference in quality, precision, and service for yourself by getting in touch with us today!